Road transport accounted for 75.3% of the total inland freight transport in EU in 2018, followed by rail freight transport (18.7%) and inland waterways transport (6.0%). In 2016, only about 54 % of the EU railway network was electrified, that means approximately 10% of the total inland freight transport in EU was transported on electrified railways.
Rail freight transport consumes up to nine times less energy per tonne kilometer than inland freight truck transport. Trains are four times more fuel efficient and they emit 75% fewer CO2 emissions. A double-track railway requires one third less land occupancy than a four-lane highway. As we mentioned above, the shifting of freight transport from roads to railways would be the fastest and most efficient way to reduce the carbon footprint in the transportation sector.
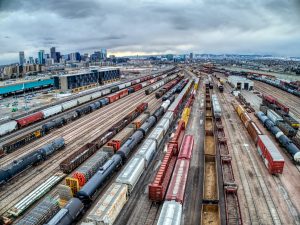
However, to shift more freight from roads to rails will not be an easy job. Let’s mention some obstacles that limit this transition. For example, the passenger trains have a priority over freight trains when it comes to access to railway infrastructure and they have a granted passage when it is necessary to clear a delay. A manager of rail infrastructure mostly wants all trains to book time slots in advance of their journey. These slots are often reserved over a year in advance of the trip. It is obvious that it is practically impossible to guarantee a time of delivery in case of freight rail transport because the freight transport has, in most cases, the lower priority. On the contrary, roads do not have any similar infrastructure manager who would need vehicles to book a certain time slot, the road vehicles can drive whenever they want. Road freight trucks do not have to worry about granting priority as all road vehicles are treated the same in case of access to road infrastructure. Train traffic has to pay for every single driven km on a railway, while trucks only pay for those parts of a road subject to toll fees. Another disadvantage for rail freight transport is a fact that the road network in EU is far bigger than the railway network, the railway density is only 1/20 of the road density. Trucks are able to deliver goods, almost whenever they want, they can provide door-to-door services very easily.
The shift a freight from roads to rails is possible, but it requires a fundamental transformation of the railway freight sector. Infrastructure capacities, railway competitiveness, cost-efficiency and productivity must be improved to achieve this modal change. It requires extensive automation, digitization of the rail freight sector and development of new vehicles and implementation of new strategies for rail freight to provide an agile delivery service. It should be considered how to develop logistics schemes like D2D (Door to door) or JIT (Just-in-time) delivery services. Since trains seldom provide D2D services, more efforts should be made to develop intermodal transport, a combination where trucks or vans perform the first and/or last mile of a railway journey. Let's have a look at some innovations which would be helpful with the mentioned shift.
A conversion from the manual world of screw coupling to automated railway operations with European Digital Automatic Coupling (DAC)
Most countries in the world have used some kind automatic coupling for a very long time. In European Union, freight wagons are still being coupled together with heavy screw coupling (except Finland and former Soviet republics of Estonia, Latvia and Lithuania where is used Soviet Automatic coupling SA3).
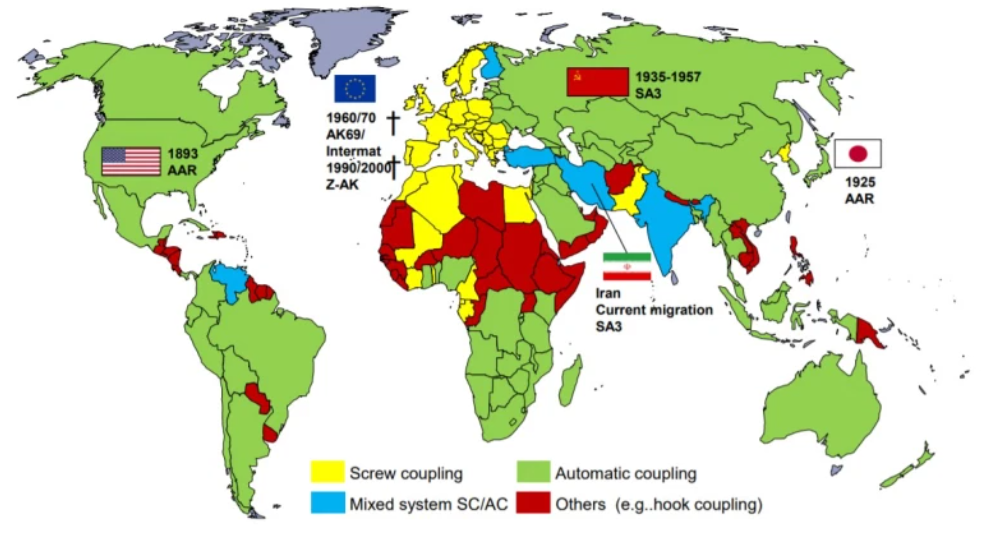
Coupling freight wagons using the screw coupling requires a hard work of manual operation. An employee has to manually hang the heavy screw coupling between the wagons, tighten the coupling and separately connect the brake lines. Screw coupling takes a lot of time and it is quite a dangerous operation (several serious accidents are already on the record). Coupling and decoupling wagons often takes place during the night, so it is not easy to find employees for this kind of operations.
With the current screw coupling used in EU, it is not possible to haul trains of over 5.000 t load (max. 3.500 t load during the starting in a slope of 12 ‰) without a risk to break the screw coupling. In case of using the UIC brake system, a brake pipe length of a train is limited to 750 m because of the physical limit in the transmission of pneumatic brake signal. Some EU countries even allow train length of 750 m, but in most of them, it is around 450 m, because of the limit of terminals, overtaking tracks, the length of stations, marshalling yards, etc. In USA, South Africa and China, trains are operated with lengths of 2500 m and in Australia with lenghts of 3000 m; that is five times more than in the EU.
Digital automatic couplers (DAC) make all connections between freight wagons (mechanical, compressed air brake, electric and data lines) without a human intervention. This is in contrast to world-wide common use of automatic couplers which only make a mechanical connection, and the brake and electric lines have to be (in most cases) connected manually. It is obvious that digital automatic couplers make coupling much faster and easier and that is a big step forward.
With digital wagon coupling, it would be possible to work together on the automatization of wagons coupling and digitization of freight transport. If a locomotive and towed wagons are equipped with sensors, it is possible to have information on the hauled rolling stock, thanks to the connection trough data cables that allows to exchange data on the entire length of the train. Here is an example on how data exchange would be helpful in a case of driving a train operation: nowadays, a train driver in a locomotive does not have any idea what is going on with the hauled freight wagons. If some wagon derailed and the train driver notices it after one or two minutes, the derailed wagon would have caused several million EUR in damage to the railway infrastructure. A scenario like that is still possible to happen even nowadays, because there is no data communication between the wagons and the locomotive. If suitable derailment indicating sensors on the wagons were installed, it would possible to avoid major damages. DAC allows the data connection between the locomotive and the wagons, as there are coupled data connectors alongside the mechanical coupling.
A consortium has been set up, known as DAC4EU and consisting of six public and private freight transport companies RCG (Austria), DB Cargo (Germany), SBB Cargo (Switzerland), and the freight wagon leasers Ermewa, GATX Rail Europe and VTG. Over the coming years, the consortium led by Deutsche Bahn AG, plans to test different digital automatic couplers. The pilot project that started in July 2020, is being financed by The Federal Ministry of Transport and Digital Infrastructure (BMVI) by approx. 13 million Euro, and will finish in December 2022. The aim is to conduct testing of the digital automatic couplers suitable for freight wagons. A dozen freight wagons were equipped with four different types of automatic digital couplers and they will be tested for a period of two years. By using the technology on a train of 24 wagons, it gets verified in the real operation. Four manufacturers are currently developing the DAC couplers, as shown on the picture on the left. The goal is to introduce digital automatic coupling throughout Europe.
The digital automatic coupling offers these advantages:
- automatic coupling and decoupling of wagons
- faster and cost-effective providing of freight transport service
- monitoring of freight wagons by sensors
- reducing labor costs
- trains with a length of more than 750 meters and a train weight over 5000 tons would be possible to operate in the EU
- allows a larger capacity of freight transport
Challenges for migration from the manual world of screw coupling to automated railway operations with DAC:
- it is necessary to convert between 432,000 EUR and 485,000 EUR freight wagons and 17,000 EUR locomotives in EU 27 plus Switzerland, Norway and the UK
- the conversion per freight wagon would costs 10,500 - 12,500 EUR and 25,000 EUR per locomotive
- the total conversion cost of freight wagons and locomotives is estimated between 4.7 and 6.2 billion EUR
- the conversion should be completed in 2030
Bimodal locomotives powered by energy from electric accumulators or diesel engines for the last mile solution
At the rail freight stations or combined transport terminals where handling cranes operate, it is not possible, for safety reasons, to have any obstacles, such as electric lines, above them. Therefore, railways in such places cannot be electrified by overhead traction wires at all.
In places like these, an electric long distance locomotive has to be decoupled from its wagons and a small diesel railroad locomotive called shunting locomotive is used for manoeuvring these wagons inside the rail transport terminals. The shunting locomotive in not intended for moving trains over long distances, but just for assembling wagons for a long distance locomotive. When the capacity of these shunting locomotives is not used sufficiently, the cost structure of rail freight transport becomes inefficient.
A possible solution would be using bimodal locomotives, suitable to haul a freight train over long distances with electric power from overhead traction lines and also for shunting services in not electrified freight terminals or in marshalling yards.
Such electric locomotive with “a last mile package” is, for example, the Traxx AC3 Last Mile locomotive produced by Bombardier Transportation, and Siemens Vectron Sr3 "Last Mile Diesel" locomotive. These electric locomotives are equipped with a small diesel engine with approx. 200-400kW power, which allows driving a heavy freight train on non-electrified lines at low speeds of 40-60 km/h, and provide the shunting operation on their own, so they would not need to use any shunting service provided by a special shunting locomotive. Thus saving money and time, of course.
Another consortium, the “Future Freight Locomotive for Europe”, has an aim of going even a step further by replacing the emission producing diesel engines by full electric last mile propulsion systems based on Li-Ion batteries, with up to 500 kWh energy and higher peak power in the range of 1MW, occupying the same space in the locomotive as the last mile diesel engine. It will bring the innovation to a next level, because it will be possible to drive a heavy freight train on short non-electrified lines and to enter areas with low noise and zero exhaust emissions requirements. In addition, the electric Li-Ion batteries will allow to recuperate large amounts of braking energy, thereby reducing the overall energy consumption.
Locomotives with the last mile functionality offer these advantages:
- The rental service of shunting locomotives at freight terminals will no longer be necessary. (however, freight terminal authorities may ban the entry with such locomotive due to a safety concern or they might charge entry fees to compensate losses for their un-used shunting service)
- Quicker access to railways in industrial sites for loading or unloading a freight
- Freight trains would make a short stop at the stations with side tracks where mobile cranes would transfer selected containers between trains, trucks or temporary storage site
An alternative freight train conception - a light freight train
The CargoSprinter is a railway freight multiple unit designed to transport freight. It was developed in 1996 by Windhoff together with cargo operators DB Cargo and Fraport. CargoSprinter consists of two motorized front and rear control cabins with five wagons (container platforms). The ends of a CargoSprinter are powered by Volvo diesel engines (265 kW), allowing it to operate on both, electrified and non-electrified railways. The wagons are permanently coupled while in service. It is a very interesting feature, that CargoSprinters can work in multiple formations, which consists of up to 7 trains, 35 wagons (630 m long). It is possible to make a formation from several CargoSprinters located at different loading stations before they come together and form one long train. Coupling CargoSprinters together takes a very short time, it can be done in minutes. As we can see, it is not necessary to do any decoupling and shunting operation; it is very easy to form a "train" which then carries the freight to its final destination.
CargoSprinter can run at high speeds (up to 120 km/h) as fast as the most of passenger trains, which allows the CargoSprinter to move on railway tracks without much impact on the movement of other trains. However, as mentioned before, passenger trains have priority over freight trains in railway access. For reasons of planning and safety, a rail infrastructure manager requires all trains to book slots in advance of their journey and these slots are often booked over a year in advance of their trip. The decisions prioritize the comfort of the passengers in all cases. If this approach could be modified or changed, rail freight transport would become more competitive to road freight transport, and providing "just in time" rail freight delivery would become more realistic.
CargoSprinter has a big advantage over common freight trains in terms of express delivery, for sure. These trains are more suitable for the smaller freight-shipments, for spontaneous and fast transport. The use of such self-propelled bidirectional trains could be an alternative to road freight transport in some special cases.
In reality, the CargoSprinter was not very successful as a commercial freight vehicle in late of 1990’s and early of 2000's, this concept was more successful as an infrastructure and services train. Nevertheless, it is a very good concept which was a way ahead of its time of introduction, but nowadays, its drawback is caused mainly by the fact that it is using a diesel powertrain. As diesel engines are the least welcomed in the world of efforts to reduce the carbon footprint, it is evident that it will be preferred for these concepts to rely more on electric power. Which brings us back to the concept of locomotives with electric motors powered by overhead rail lines and from a Li-ion battery pack to have the "last mile" functionality for accessing the non-electrified rail sidings or rail freight terminals.
This concept offers a change in rail freight transportation, allowing rapid transport of freight, in the cases of less than full trainload or short line freight.
Related articles
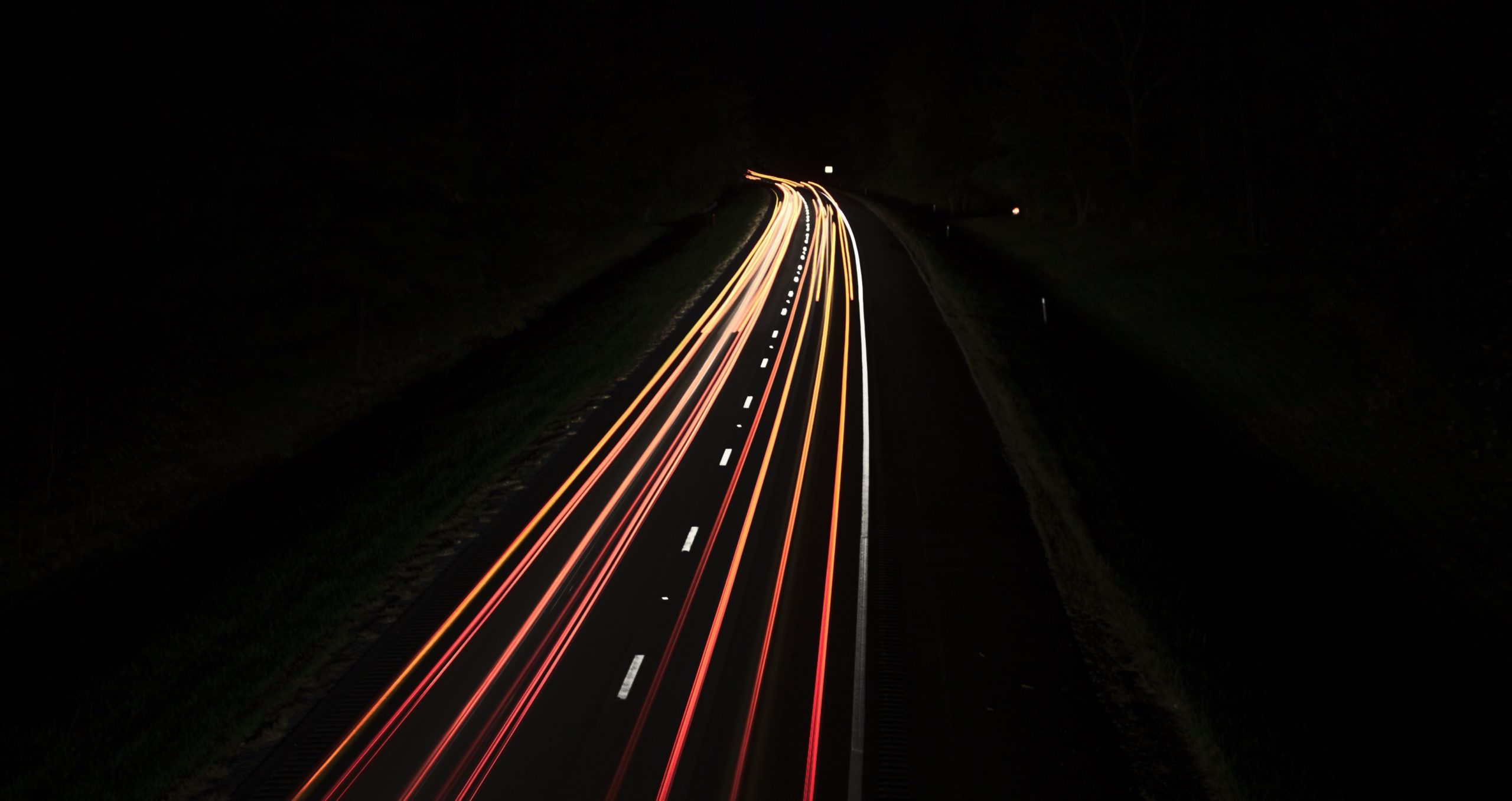
Slovakia Is Working Its Way into Battery Industry
8. March 2021
Slovakia is following the trend by making progress in development and production of electric car batteries. After launching of a new smart battery for electric cars by InoBat Auuto, the National Battery Centre was established.
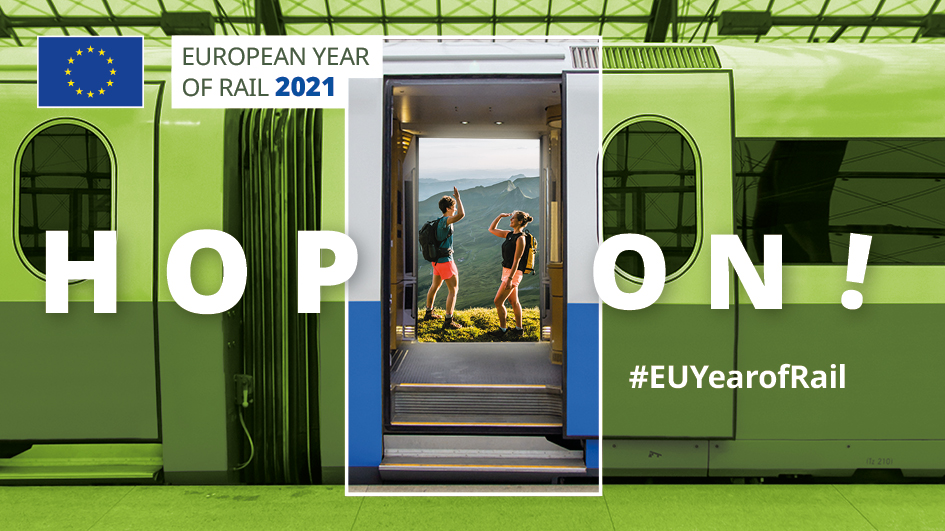
2021 is the European Year of Rail
8. March 2021
The European Commission has designated the year 2021 to be the European Year of Rail. Throughout the year, a variety of events and stimuli to motivate passengers and freight to increase their rail transport will be planned.
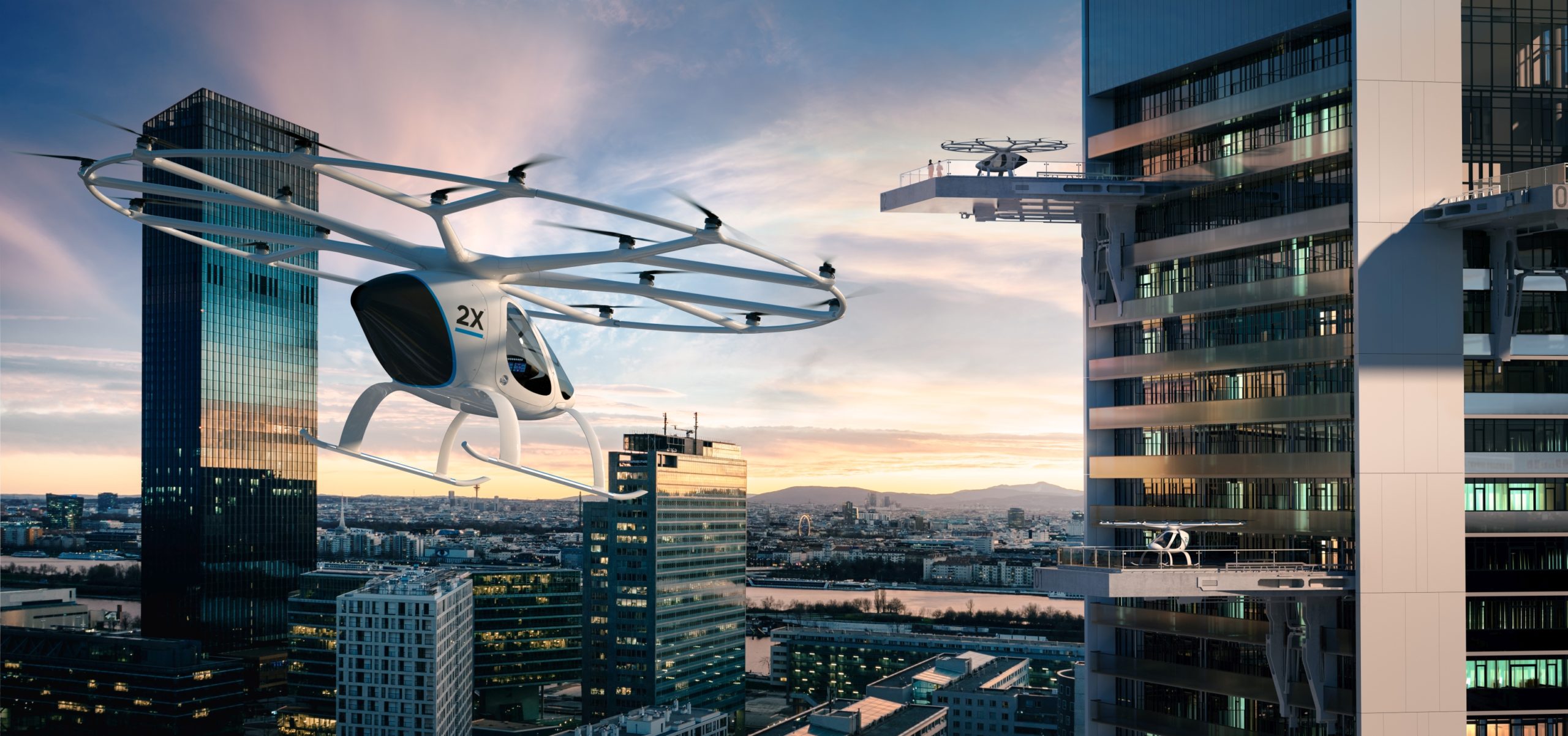
Recent Breakthroughs in Air Mobility
27. February 2021
Austria, as the first country in the European Union, has permitted a trial operation of an automated drone. The EHang Company from southern China has ambitions to become one of the global platforms for autonomous, ecological, and safe air taxis.